Key Highlights
- This article compares and contrasts the properties, applications, and costs of aluminum alloys 3003 and 6061.
- It examines the chemical composition and mechanical properties of each alloy, highlighting their strengths and weaknesses.
- 3003 aluminum is known for its excellent formability, good corrosion resistance, and affordability, making it suitable for applications where high strength is not critical.
- 6061 aluminum, on the other hand, offers higher strength, good weldability, and versatility, finding applications in demanding industries like aerospace and automotive.
- The blog post provides a comprehensive analysis to help readers determine the best aluminum alloy for their specific needs.
Introduction
Aluminum alloys are used a lot in different industries. This is because they are lightweight, strong, and resist corrosion well. Among the many aluminum alloys, 3003 and 6061 are some of the best. They are especially known for their strength and durability. This blog post will compare aluminum 3003 and 6061. It will look at their main characteristics, benefits, and the best ways to use them in structural applications.
Exploring the Basics of Aluminum 3003
Aluminum 3003 is part of the 3000 series of aluminum alloys. These alloys do not get stronger through heat treatment. Aluminum 3003 is well-known for being easy to shape and mold. This formability allows it to be used for complex designs. Manganese is the main alloying element in this metal. It makes aluminum 3003 stronger than pure aluminum while keeping it easy to work with.
Aluminum 3003 also has good corrosion resistance, especially in outdoor conditions. This makes it a good choice for outdoor uses. Its low cost and ease of making have made it popular in various industries. You can find it in construction, transportation, packaging, and consumer goods.
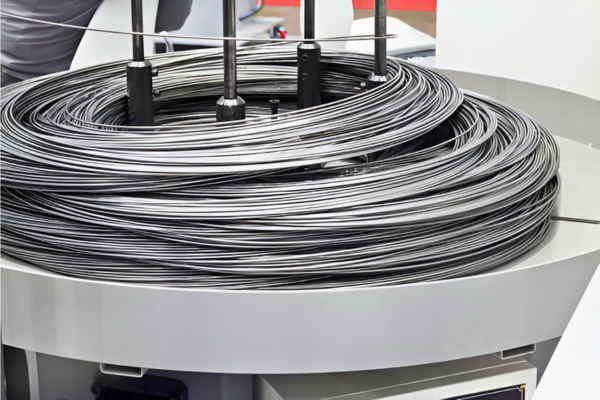
Key Properties of 3003 Alloy
One key feature of 3003 aluminum is its excellent formability. It bends, shapes, and draws easily. This makes it perfect for parts that need complex shapes. Its low yield strength and high ductility let it change shape a lot without breaking.
Also, 3003 aluminum has good corrosion resistance. It does well in normal air and many industrial settings. We can make this resistance even better with surface treatments like anodizing, which adds a protective oxide layer.
In addition, 3003 aluminum is good for welding. We can use common arc welding methods easily. Its chemical mix helps reduce the risk of cracking when welding, especially compared to some heat-treatable alloys.
Chemical Composition of 3003
The chemical makeup of aluminum 3003 is important for its features. Like all aluminum alloys, it is mostly made of aluminum, making up more than 90% of its weight. The rest includes alloying elements that affect its properties.
Manganese is the main alloying element in aluminum 3003. It usually ranges from 1.0% to 1.5%. This manganese helps to increase strength and gives it some ability to harden when worked, compared to pure aluminum.
Along with manganese, small amounts of other elements can be there. These may include copper, iron, silicon, and zinc. Keeping these minor elements in check helps improve special features like machinability and corrosion resistance.
Chemical Element | Content (%) |
Aluminum (Al) | 96.7% – 99% |
Manganese (Mn) | 1.0% – 1.5% |
Copper (Cu) | 0.05% – 0.20% |
Iron (Fe) | 0.70% max |
Silicon (Si) | 0.60% max |
Zinc (Zn) | 0.10% max |
Others | 0.05% max each, 0.15% total |
Typical Applications of 3003 Aluminum
The mix of features found in 3003 aluminum makes it a great option for many industries and uses. It is popular for its decent strength, ease of shaping, resistance to rust, and affordable price.
Because of its ability to be shaped easily and resist rust, 3003 aluminum is commonly used in the food industry. Cooking tools such as pots, pans, and trays often use this alloy. It can handle heat well and prevent damage from food acids.
Some other common uses are:
- General sheet metal work: Roofing panels, siding, gutters, downspouts
- Chemical equipment: Storage tanks, processing equipment
- HVAC components: Ductwork, heat exchangers
- Packaging: Cans, bottle caps
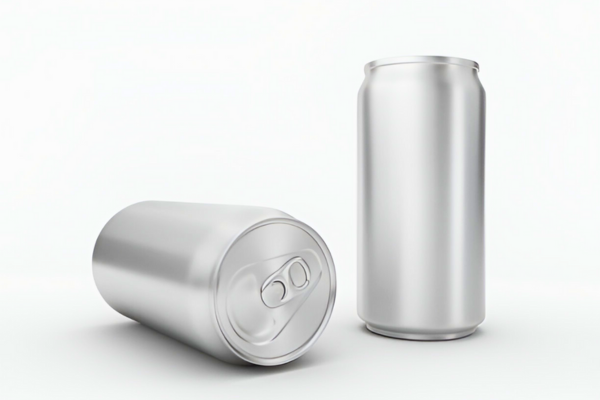
Diving Into the Characteristics of 6061 Aluminum
6061 aluminum is an alloy from the 6000 series. It is well-known for its ability to be treated with heat. This heat treatment helps it gain much higher strength. This strong features is due to the key alloying elements, which are silicon and magnesium. These elements make it highly versatile and widely used.
6061 aluminum is widely used in many places. It is used for structural components in buildings and bridges. It is also found in complex parts for aircraft and cars. This alloy is well-suited for demanding jobs because it offers great strength, good weldability, and strong corrosion resistance.

Core Features of 6061 Alloy
One great thing about 6061 aluminum is its strong strength, especially when it is heat-treated to its T6 temper. When we compare it to 3003, 6061 has higher yield and tensile strengths. This means it can handle more loads and stress.
Besides being strong, 6061 aluminum is also very easy to weld. You can use different welding methods like MIG, TIG, and arc welding to join it. However, it is essential to control the heat well during welding. This is important to avoid losing strength in the areas affected by heat.
What makes 6061 aluminum special is its versatility. It has a good mix of strength, excellent weldability, machinability, and corrosion resistance. Because of these properties, it can be used in many different applications across various industries. This shows that it is a truly multi-purpose alloy.
Chemical Composition of 6061
6061 aluminum is known for its great features, which is because of its balanced mixture of chemicals. Like other aluminum alloys, it has over 95% aluminum in it. The rest includes other important alloying elements that help create its unique qualities.
Silicon and magnesium are the main alloying elements in 6061 aluminum. They usually have ranges of 0.4% to 0.8% for silicon and 0.8% to 1.2% for magnesium. Together, they form magnesium silicide (Mg2Si). This is important because it makes the alloy heat-treatable, which raises its strength.
Apart from silicon and magnesium, there can be small amounts of copper and chromium in 6061 aluminum. These tiny additions help improve certain features like machinability and corrosion resistance. For example, copper helps create a finer grain structure, which is good for machining abilities.
Chemical Element | Content (%) |
Aluminum (Al) | 95.8% – 98.6% |
Magnesium (Mg) | 0.8% – 1.2% |
Silicon (Si) | 0.4% – 0.8% |
Iron (Fe) | 0.7% max |
Copper (Cu) | 0.15% – 0.40% |
Chromium (Cr) | 0.04% – 0.35% |
Zinc (Zn) | 0.25% max |
Manganese (Mn) | 0.15% max |
Titanium (Ti) | 0.15% max |
Others | 0.05% max each, 0.15% total |
Common Uses of 6061 Aluminum
6061 aluminum is popular because it is strong but light. This makes it very useful in transportation, especially in cars and planes. It’s lightweight and helps save fuel while still being strong.
The construction industry also makes good use of 6061 aluminum. It is used in buildings and bridges, as well as in railings and ladders. Its strength, resistance to corrosion, and ability to be welded make it a favored option.
Here are some common uses of 6061 aluminum:
- Aerospace: Parts of aircraft like wing components and fuselage sections.
- Automotive parts: Components like wheels, chassis elements, and engine parts.
- Structural components: Items like beams, columns, and trusses.
- Recreational equipment: Gear like bicycle frames, parts for boats, and fishing reels.
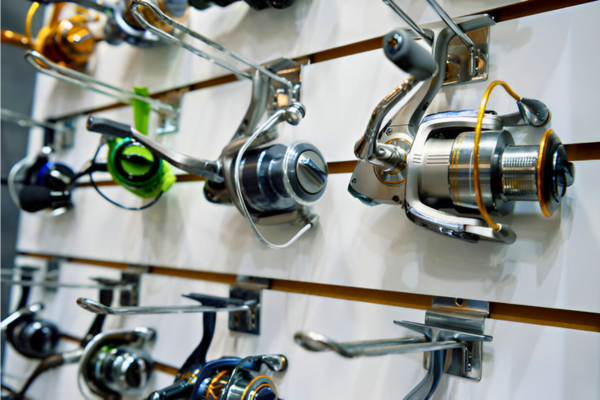
Head-to-Head Comparison: 3003 vs. 6061
We have looked at the individual features of 3003 and 6061 aluminum alloys. Now, let’s compare them directly to see how they differ and where each is best used. Both alloys have their own strengths, but they are best for different jobs based on what the project needs.
Knowing these differences is important when picking materials for different engineering and manufacturing tasks. In the next sections, we will take a closer look at their mechanical properties, workability, costs, and other factors. This will help us figure out which alloy is the better choice for specific situations.
Comparing Mechanical Properties
When it comes to mechanical properties, a stark contrast exists between 3003 and 6061 aluminum alloys. 6061 emerges as the clear winner in terms of strength, boasting significantly higher yield strength, tensile strength, and hardness, particularly in its heat-treated T6 condition.
Yield strength, the point at which permanent deformation occurs, is notably higher in 6061, exceeding that of 3003 by a substantial margin. This difference highlights 6061’s ability to withstand higher loads before undergoing plastic deformation.
Below is a table offering a concise comparison of key mechanical properties:
Property | 3003-H14 | 6061-T6 |
Yield Strength (psi) | 17000-24000 | 35000-40000 |
Tensile Strength (psi) | 22000 | 42000 |
Hardness (HB) | 40 | 95 |
Analysis of Formability and Weldability
While 6061 is strong, 3003 is better when it comes to formability. It bends, shapes, and forms easily into complex designs without needing special tools. This makes 3003 a great choice for things like detailed panels or curved parts.
Both alloys can be welded well. However, 3003 has a slight advantage. It is less likely to crack during cooling. Still, 6061 can be welded successfully if we control the heat properly and use the right filler materials.
When picking between 3003 and 6061, it’s important to think about what we need for the project. If we need good workability and easy forming, 3003 is the best choice. If we need higher strength and the ability to handle high stress, 6061 is the better option.
Cost comparison between aluminum alloy: 3003 vs. 6061
In terms of cost, 3003 aluminum is usually cheaper than 6061. The lower price comes from a few reasons. First, making 3003 is a simpler process. Also, it does not need heat treatment, which costs more.
Even though 3003 is more affordable, it’s important to look at what the project needs. If we need more strength, durability, or special features from 6061, paying more can be worth it later. The best way to find the right choice is to balance the material cost with what we need and how much we might save in the future with each alloy. GET A QUOTE
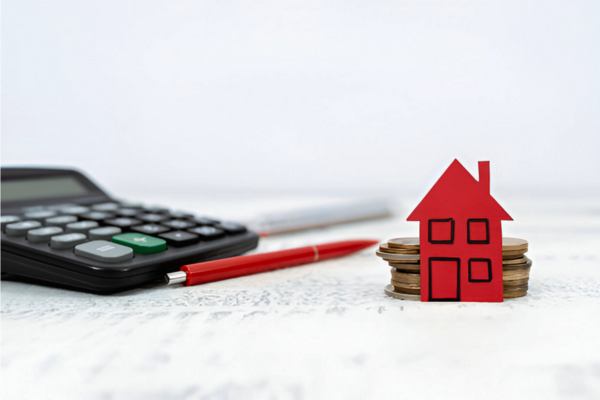
Conclusion
In conclusion, it is important to know the differences between Aluminum 3003 and 6061 alloys. This knowledge helps us make good choices for various uses. Aluminum 3003 has certain benefits in terms of its properties and applications. On the other hand, 6061 has its unique features and uses. Comparing their mechanical properties, formability, weldability, and cost offers useful information for picking the right alloy. Both alloys have their own strengths, whether you need to value cost or specific performance. If you have more questions or need help choosing the best alloy for your project, please reach out to us.
At Linsy Aluminum, we are a leading aluminum supplier and manufacturer in China. Our cutting-edge aluminum factory delivers top-quality, durable, and cost-effective solutions for various industries. Here’s why we stand out:
- Superior Quality: We ensure precision and reliability in every product.
- Competitive Pricing: Affordable solutions without compromising on performance.
- Global Reach: Trusted by clients worldwide, from construction to automotive.
As one of the best aluminum brands in China, we combine innovation, quality, and sustainability to meet your specific needs. GET A QUOTE