This guide looks at two common aluminum alloys: 2024 and 7075. These alloys are great options because they are strong and offer price advantages in their pricing, along with impressive mechanical performance. These alloys are used in the tough aerospace industry and other industry applications. By learning about their special traits and differences, you can choose better for your engineering projects.
What are the differences between 2024 and 7075 aluminum alloys?
The 2024 aluminum alloy is an ideal alloy choice when you need an excellent strength balance between strength and weight. In contrast, the 7075 aluminum alloy has lower corrosion resistance and is stronger, but it doesn’t resist corrosion as effectively. Because 7075 is tougher and stronger than 2024, it is ideal for aerospace applications where strength is crucial.
The lower costs of 2024 aluminum alloy are attractive for projects that do not need high strength. However, you should consider what your project requires. It is vital to balance performance with your budget. Spending more on 7075 aluminum alloy is often a smart choice for projects that demand the highest strength and durability.

Understanding 2024 Aluminum Alloy
The 2024 aluminum alloy is one of the strongest choices available. Many people see it as a great pick when they need strength and ease of use. This is why several aircraft parts are made with this alloy. It proves that it works well under pressure.
The alloy contains a lot of copper. This gives it strength and helps it wear down less over time. It also shapes well during processing. However, it does not fight corrosion very well. This is something you should think about. Still, using protective methods can help reduce this issue.
Origins and Composition
The 2024 aluminum alloy primarily has copper in it. This copper gives the alloy strength and hardness. It also improves how the alloy performs during heat treatment.
The copper in the alloy helps it resist corrosion, especially in wet places. To fix this problem, a protective layer is added on top. This layer is usually made of pure aluminum oxide and covers the open surfaces.
This strength and rust protection mix makes the 2024 aluminum alloy useful in many areas. It provides a great balance of performance and durability. GET A QUOTE
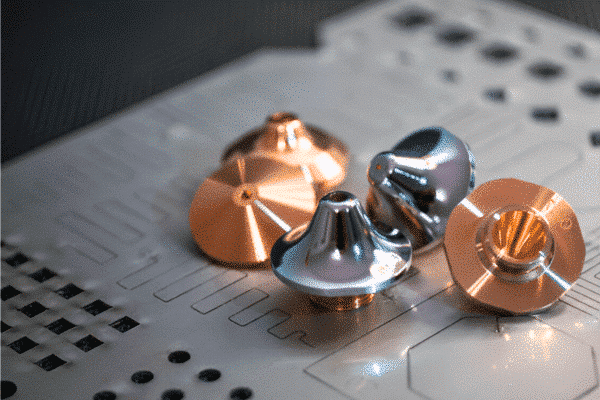
Key Properties and Applications
The 2024 aluminum alloy is perfect for projects that need strong materials. It also offers good resistance to wear. You can often find it in the aerospace industry. This alloy makes important parts like aircraft structures, wings, and fuselage components.
However, in some spots, it can be vulnerable to stress corrosion. This means we need to consider where to use it carefully. It’s really important to take protective measures in marine environments or harsh chemical areas.
The 2024 aluminum alloy is a strong choice for projects that require strength and resistance to wear over time. This is very important in the aerospace industry. Make sure to include protection against corrosion when needed.
Diving into 7075 Aluminum Alloy
7075 aluminum alloy is very strong for its weight. It is one of the strongest aluminum alloys out there. You can often find it in military applications and aerospace settings. This alloy does a great job handling tough structures.
The 7075 aluminum alloy is very strong. This is due to its high zinc content. This gives the alloy strength and durability. It performs well in difficult conditions.
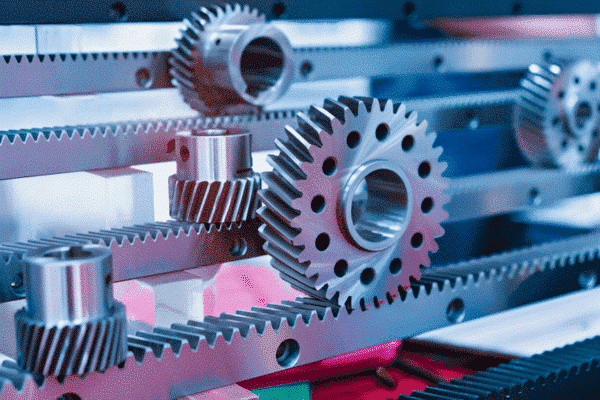
Development and Chemical Makeup
The 7075 aluminum alloy is an important step in material science. It is well-known for its high strength. Zinc is a major reason for this strength, which helps make the alloy even stronger.
7075 has zinc and magnesium in its makeup. Magnesium makes it stronger and harder. When combined, these elements enhance its mechanical properties. Because of this, 7075 is excellent for strong structural uses.
Adding copper and chromium can help improve performance. This makes it easier to adjust to the needs of various industries.
Distinct Characteristics and Applications
7075 is one of the strongest aluminum alloys. This makes it very useful in places where strength matters a lot. You can often see it used in aircraft structures and military gear. Its strong nature helps it handle tough situations.
7075 aluminum alloy is very strong and has good fatigue resistance. This means it works well when it is put under repeated stress. This feature is key for parts that go through many cycles of strain.
The 7075 aluminum alloy is very strong and hard and helps resist wear. This is why it is a great option for key parts in aerospace. It is also perfect for top-quality sports equipment and other high-performance projects.
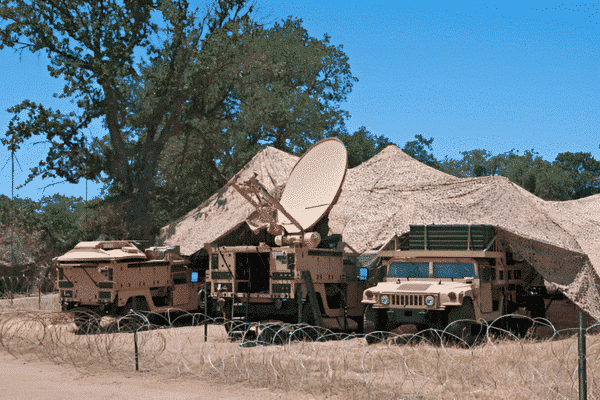
Comparative Analysis of Mechanical Properties
A close look at the mechanical properties of 2024 and 7075 aluminum alloys shows important differences. These differences help decide which alloy is best for specific tasks.
When we check tensile strength and fatigue resistance, we see that each alloy has its strengths and weaknesses. Understanding these qualities helps us find the best uses for each alloy in different tasks.
Property | 2024 Aluminum | 7075 Aluminum |
Main Alloy Element | Copper | ZInc |
Tensile Strength | 400-450 MPa | 540-570 MPa |
Yield Strength | 270-310 MPa | 480-510 MPa |
Density | 2.78 g/cm³ MPa | 2.81 g/cm³ |
Property | 120 HB | 150 HB |
Strength and Durability Differences
7075 aluminum alloy is strong. It has high tensile strength. This means it can handle strong forces without bending or getting damaged. This ability is very helpful for tough construction projects.
Yield strength is a key factor to consider. It shows how much stress a material can handle before it bends or permanently changes shape. In this case, 7075 is stronger than 2024. This means it can take a lot of pressure without failing.
7075 has better fatigue strength. This means it is less likely to crack or break when under repeated stress. This is very important for parts used in aerospace and automotive fields. These parts deal with regular movements and changes. GET A QUOTE
Flexibility and Weight
7075 is stronger than 2024. However, 2024 is more flexible and easier to handle. It has a lower yield strength. This means it can bend more easily. Because of this, it is simpler to shape and form it without losing its strength.
This extra flexibility and good machinability make creating detailed designs and complex shapes easier. The material properties of 2024 help in making the manufacturing process simpler.
Both alloys are strong and light, giving them a high strength-to-weight ratio. This means they are good options for jobs requiring sturdy but lightweight materials. However, 2024 is lighter than the other one. Therefore, it is the better choice to keep the weight very low.
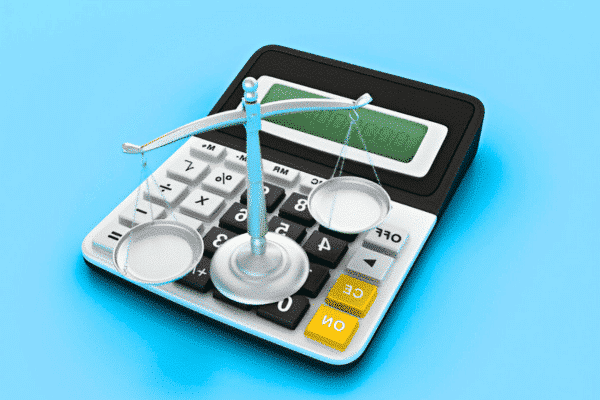
Thermal and Electrical Conductivity
Both 2024 and 7075 aluminum alloys do not keep heat. This is mainly because aluminum is good at moving heat around.
There are small differences in the mixtures of their alloys. These differences can change how well they conduct heat and electricity. Even though these changes are minor, they can affect which high-temperature or electrical jobs each alloy is best for.
Heat Treatment Responses
Heat treatment is important for making alloys stronger. It can improve their mechanical properties. One method, called precipitation hardening, can increase their strength and hardness. This helps the alloys perform better in tough conditions.
The 2024 and 7075 alloys react differently to heat treatment. This change affects their final properties and their uses. Both alloys gain benefits from heat treatment. However, 7075 alloys become much stronger after heat treatment than 2024 alloys.
This change in how materials respond to heat treatment shows why you must choose the right one for the task. Engineers can select the best material to fit specific needs when they know these differences.
Conductivity for Electronics
Understanding how different alloys work with electricity is important. They may not be the first choice for electrical jobs. However, the combination of materials in an alloy can change how well it carries electric current.
7075 and 2024 aluminum alloys have average electrical conductivity. This means they are good for specific electrical tasks. They perform well, especially when the strength of the material and weight are more important than how well they conduct electricity.
When you need good electrical conductivity, copper is often the best choice. It’s important to consider how conductivity, weight, strength, and cost work together when deciding which material to use for electrical needs.
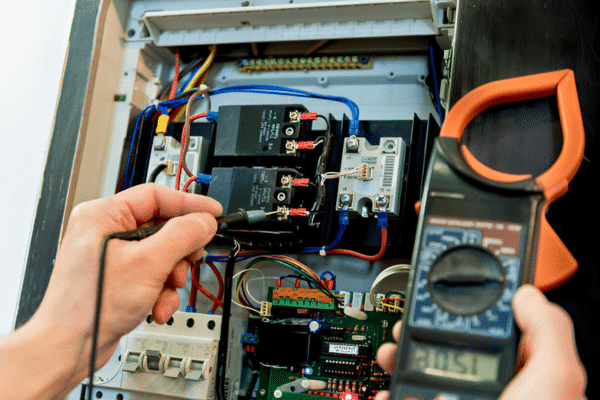
Manufacturing Processes and Machinability
Both 2024 and 7075 aluminum alloys can be used for different manufacturing methods like extrusion, forging, and machining. They each have unique traits. You should think about these traits carefully when making products.
How we machine, shape, and weld these materials depends on their unique features. Knowing these differences is important. It helps improve the manufacturing process. It also makes sure the parts are made right. GET A QUOTE
Formability and Workability
When we talk about workability and formability, the 2024 aluminum alloy stands out. It is simple to bend, shape, and form. This feature makes it perfect for parts that have complex shapes.
2024 is simple to cut, drill, and shape. This is because it has good machinability. It offers more options for designing and making products. This ease can also help lower production costs.
7075 is a strong alloy. However, it can be difficult to machine and shape. Its hardness makes it tough to work with. To handle this alloy correctly, you usually need special tools and techniques.
Cutting and Welding Techniques
Both alloys can be cut using regular tools, such as a saw or waterjet cutter. The choice of method may affect the final quality. It might also lead to distortion, especially because 7075 is harder.
Welding these alloys, especially 2024, needs special measures. We must be careful about the heat we use to avoid problems like cracking. Choosing the right filler materials is also important to ensure good welding.
Both alloys can be used in many manufacturing processes. But 2024 is usually easier to work with. It has good machinability and formability. On the other hand, 7075 may need special tools and techniques to get better results.
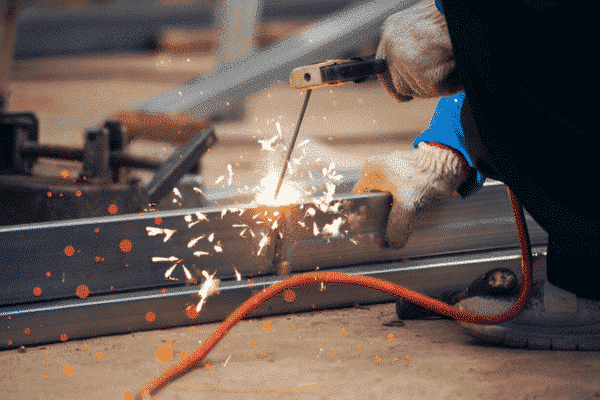
2024 vs 7075 Aluminum Yield Strength
Yield strength is an important feature of materials. It shows how much stress a material can handle before it permanently changes shape. In this example, 7075 aluminum alloy is stronger than 2024 aluminum alloy. The 7075 alloy can take more stress without losing its original shape.
These alloys differ in how they are made and what is inside them. The strong part of 7075 alloys is zinc. This gives it a higher strength-weight ratio and good mechanical properties, which are close to that of a Titanium alloy. Silicon is also key in many aluminum alloys produced in China. On the other hand, the 2024 aluminum alloy is not as strong. Still, it does a good job when faced with repeated stress. So, 2024 is a good choice when you do not need the strongest material.
2024 vs 7075 Aluminum Hardness
Hardness tells us how well a material can handle scratches or pressure. It is important for its strength, toughness, and how long it will last. The 7075 aluminum alloy is harder than the 2024 aluminum alloy. But, its temper shows it has lower strength. This means it can resist wear on its surface more and is less likely to get damaged.
The higher hardness of 7075 can make it tough to machine. Its thermal conductivity is key for rapid heat dissipation and cooling quickly when higher temperatures are high. It needs special tools and techniques for cutting and shaping, which raises manufacturing costs. On the other hand, 2024 exhibits better machinability, making it simpler to work with and letting designers create more complex shapes.
2024 vs 7075 Aluminum Modulus of Elasticity
The modulus of elasticity, also called Young’s modulus, helps us understand how stiff a material is. It shows how well a material can resist changes when stressed. The 2024 and 7075 aluminum alloys have a similar modulus of elasticity. It is measured in gigapascals (GPa). This means both materials have a similar level of stiffness.
Both alloys act the same way when they feel the same pressure. They will bend in the same way, even if their strengths are different. 7075 can take a stronger load of around 280 MPa before it changes shape permanently. However, both materials resist shape changes similarly while they are still elastic.
2024 vs 7075 Aluminum Price
Price matters when picking materials. A look at prices shows clear differences between 2024 and 7075 aluminum alloys. Generally, 7075 aluminum alloy costs more. This is because it is stronger and has better corrosion resistance. GET A QUOTE
Which alloy, 2024 or 7075, is better for aerospace manufacturing?
2024 is better for extrusions and other shapes, while 7075 is preferred for thicker plate applications due to its higher strength. 7075 offers better stress corrosion cracking resistance, but 2024 has better formability. The choice depends on the specific requirements of the aircraft components.
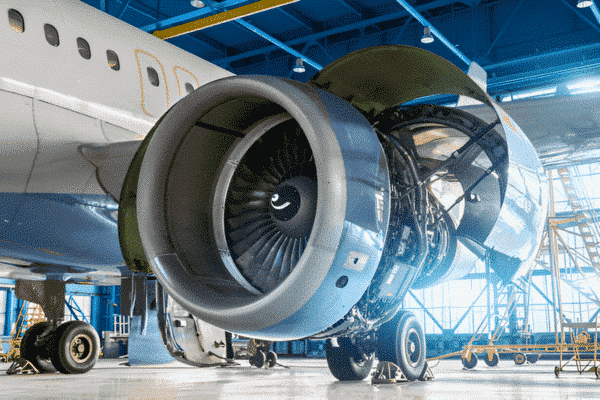
Conclusion
In conclusion, knowing how 2024 and 7075 aluminum alloys differ is important. This information helps you make good choices in different industries. The 2024 alloy is flexible, while the 7075 alloy is strong and lasts longer. Depending on what you need, one alloy might be better. When you decide, consider things like mechanical properties, machinability, and price. If you need more help picking the right aluminum alloy for you, feel free to contact our experts.
Why Choose Us
At Linsy Aluminum (Premium Alu), we pride ourselves on being China’s top aluminum supplier and factory. We offer high-quality aluminum alloys like 2024 and 7075, which are ideal for industries such as aerospace and automotive.
Our commitment to quality, competitive pricing, and timely delivery makes us one of the best aluminum brands in the market. Whether you need strong, durable materials or more flexible alloys, we provide expert guidance to help you find the right solution for your project.
Choose Linsy Aluminum (Premium Alu)—trusted for excellence and customer satisfaction.