Key Highlights
- 7050 and 7075 are strong aluminum alloys. They are used for tough jobs, especially in the aerospace industry.
- 7050 offers excellent stress corrosion resistance, great fatigue strength, and good fracture toughness. This makes it great for thicker sections and important structural parts.
- 7075 has higher tensile strength and yield strength. This means it is very strong for its lightweight.
- The machinability of 7075 is slightly better than 7050, but 7050 has better thermal conductivity.
- Both alloys can be heat-treated to improve their mechanical properties. Common tempers for these alloys are T6, T73, and T74.
- Even with small differences, both alloys are top choices. They tend to be more expensive than other aluminum alloys.
Introduction
This guide will explain the main differences between 7050 and 7075 aluminum alloys. Both alloys are strong and lightweight, and they are known for their superior strength as well as being classified among the highest strength aluminum alloys commercially available. Their highest tensile strengths are about 510 MPa. However, 7075 aluminum has a higher yield strength. These alloys are often used in tough structural applications, especially in the aerospace industry. They are great for making strong structural parts. It is important to know their special properties, strengths, and limits.
Understanding 7050 and 7075 Aluminum Alloys
7050 and 7075 aluminum alloys are part of the 7000 series. They are known as aerospace-grade aluminum alloys because they have excellent strength and good resistance to exfoliation and fatigue. The makeup of these alloys is similar, but small differences in the alloying elements create different performance characteristics that meet specific requirements. Both alloys are popular for lightweight uses because of their low weight and high strength. They are widely used in aircraft structures, sporting goods, and high-performance vehicles.
These alloys can be heated to improve their mechanical properties. However, they are usually not good for welding and have average machinability. It’s important to understand this when selecting between 7050 and 7075 for a certain use.
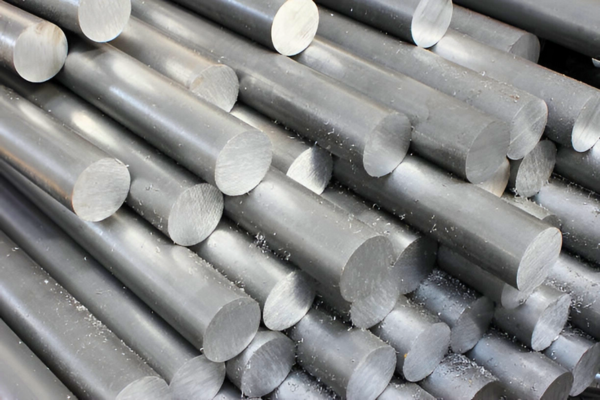
Composition and Basic Properties of 7050 Aluminum
The 7050 aluminum (Al) alloy has elements like zinc, magnesium, manganese, titanium, and silicon. These elements give it high strength and help it resist fatigue. When copper is added, the alloy gets even better. It improves the alloy’s properties and makes machining easier. A big advantage of the 7050 aluminum alloy is its strong ability to resist stress corrosion cracking. This makes it perfect for tough environments.
Adding zirconium to the alloy makes it stronger. It also helps stop cracks from spreading. To achieve the best properties, the 7050 alloy is usually heat-treated. The most common tempers for this alloy are T7451 and T7351. These tempers are known for their high strength and good stress corrosion resistance.
Composition and Basic Properties of 7075 Aluminum
7075 aluminum alloy has zinc, magnesium, and copper, just like 7050. It has more zinc, which makes it stronger. Adding chromium helps it resist corrosion. This is important in areas where stress corrosion might happen.
7075 aluminum is well-known for being strong and light. It is stronger than many other types of aluminum. This aluminum has several tempers. The T6 and T651 tempers are popular choices. People choose them because they have high strength and good machinability.
Physical and Mechanical Property Comparison
7050 and 7075 aluminum alloys are very similar in what they are made of and how they are used. However, they have slight differences in their mechanical properties. These small differences affect how well each alloy works for certain tasks.
Engineers and manufacturers need to understand these differences. They should select the right material based on how it performs. This ensures that the final product is good quality and dependable.
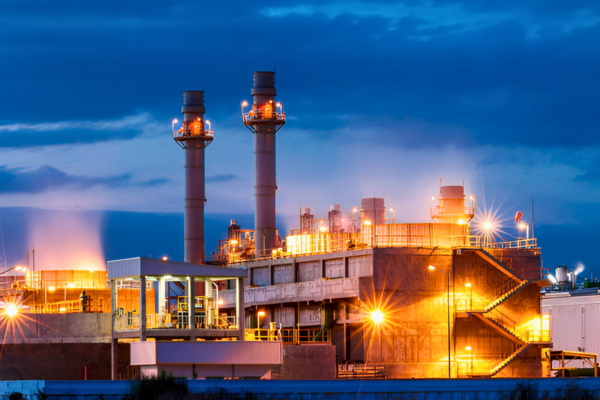
Strength and Durability Differences
When we discuss strength, 7075 is stronger than 7050. It can withstand greater stress before permanently deforming. Also, 7075 has a higher tensile strength. This means it can handle more force without breaking.
On the other hand, 7050 has better toughness, especially when it’s around seawater. This means it can stop cracks from spreading and does not easily change shape. Because of this, 7050 is a great choice for structural components where cracks could lead to big problems, especially under repeated stress. Therefore, while 7075 is usually stronger, 7050 has better fracture toughness and can recover from unexpected cracks.
Thermal Conductivity and Heat Treatment Variations
The 7050 aluminum alloy conducts heat a bit better than the 7075 alloy. This matters when a piece of aluminum needs to cool down well because it also has good electrical conductivity. This can be found in components such as heat sinks and engine parts. Both alloys can be heat-treated. This treatment improves their mechanical properties. It helps them reach the strength and hardness needed.
The heat treatment for both alloys has several steps. These steps are solution treatment, quenching, and aging. The exact temperatures and the time for each step can vary. This depends on the temperature and what the application requires. A good example is the T6 temper. It comes from artificial aging. This temper is common for both alloys and makes them stronger.
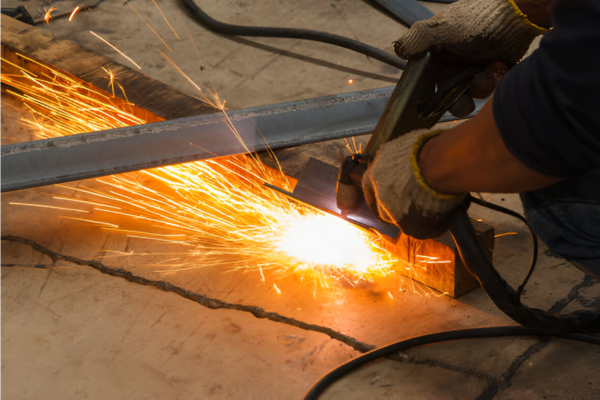
Corrosion Resistance Differences
Both alloys are good at preventing corrosion, but they are different in some ways. The 7050 aluminum alloy is better at resisting stress corrosion compared to the 7075 alloy. This makes the 7050 a better option for tough spots, like near the sea or in places with chemicals.
The 7075 alloy is recognized for its good corrosion resistance. Still, it may have a higher chance of stress corrosion cracking, especially in its strongest forms called tempers. To lower this risk, 7075 is usually coated with a more corrosion-resistant aluminum alloy, like pure aluminum. This coating provides a protective layer.
Common Tempers Differences
Both 7050 and 7075 alloys are available in several tempers to meet different specifications and needs, complying with standards such as ASTM. The 7050 alloy typically has T7451 and T7351 tempers. In contrast, the 7075 alloy is usually found in T6, T651, and T73 tempers. Each temper undergoes a heat treatment process. This process gives the alloy special mechanical properties.
T6 tempers in both alloys have high strength. This is one reason they are favored for structural components in aerospace applications. When picking the right temper, we need to find a good balance of strength, toughness, corrosion resistance, and other important factors based on how they will be used.
Applications and Industry Usage
The special features of 7050 and 7075 aluminum alloys are important for many industries. Each industry has different needs to work well. The decision to use one of these alloys often depends on the requirements of the project.
Aerospace and Aviation Applications for 7050 and 7075
Both 7050 and 7075 aluminum alloys are widely used in the aerospace industry.
7050 is known for its strong resistance to fatigue and good stress corrosion. This makes it a popular choice for important parts of airplanes. These parts include wing skins, fuselage frames, and bulkheads.
It can handle a lot of stress and won’t crack under pressure. This makes it a great option for parts that experience a lot of stress during flights.
7075 has a strong strength-to-weight ratio. This makes it a good choice for aircraft parts. It is used in structural components like landing gear and wing spars.
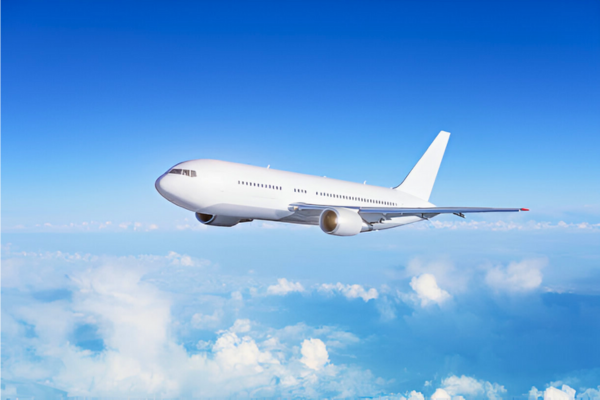
Automotive and Structural Applications Differences
Both 7075 and 7050 alloys are used in aerospace. They are also found in cars and other strong buildings.
7075 is a really strong material. This strength makes it ideal for parts in high-performance cars, such as the suspension and chassis. Many bicycle frames are also made from 7075. Its lightweight feature helps save fuel while still being durable.
7050 is great for reducing stress and preventing breaks. It is a strong option for tough work like building bridges, pressure containers, and parts for heavy machines. It can manage high stress and regular use. This helps keep things safe and reliable over time.
7050 vs 7075 aluminum alloys Price Comparison
The prices for 7050 and 7075 aluminum alloys rely on how much people want them, the price of the raw materials, and how difficult the processing is. Typically, both alloys are viewed as high-quality options. This is mainly because they have good performance characteristics compared to other aluminum alloys.
The price gap between 7050 and 7075 is often small. But, 7050 may be a bit more expensive than 7075. This is due to its better stress corrosion resistance and stronger fatigue features. Prices can change based on market conditions and order sizes. Therefore, it’s a good idea to check with suppliers for the most recent details. GET A QUOTE
Conclusion
In conclusion, it’s essential to understand the differences between 7050 and 7075 aluminum alloys. The 7050 alloy is strong in some areas, while the 7075 excels in others. Both alloys serve specific purposes in industries like aerospace, automotive, and structural engineering. Picking the right aluminum alloy can make your products work better and last longer.
At Linsy Aluminum (Premium Alu), we are a trusted aluminum supplier in China, known for offering high-quality aluminum alloys like 7050 and 7075. As one of the best aluminum brands, we provide durable, high-performance materials tailored to your needs, whether for aerospace, automotive, or structural applications. With competitive pricing, customizable options, and efficient delivery, our aluminum factory in China ensures you get reliable products and exceptional service to meet project deadlines. Choose us for quality, performance, and trust in every order. GET A QUOTE