Key Highlights
- aluminum alloy 5052 is a flexible material. It is strong and resists corrosion. Plus, it can be easily shaped.
- This alloy is especially useful in marine environments because it can resist saltwater corrosion.
- Its lightweight strength makes it popular in the automotive and aerospace industries.
- Aluminum 5052 also has good weldability and machinability. This means it works well in various manufacturing methods.
- It comes in several tempers, which allows us to change its properties for different applications.
Introduction
Aluminum Alloy 5052 is a strong and flexible material. It resists corrosion well and is tough against wear. Because of these qualities, many industries like to use it. This alloy is recognized by the aluminum association for its high magnesium content, which is the main element that makes it strong. It can be welded easily, and it has good mechanical properties. Because of this, it works well in products like appliances and structures.
To use it well, we should know its specifications, impurity levels, and tempers. These details are important for meeting specific mechanical property requirements. This aluminum alloy remains stable at room temperature and in seawater. This stability is another reason why it is a great choice. Let’s look more closely at what makes this aluminum alloy unique, its composition, and its application in different fields.
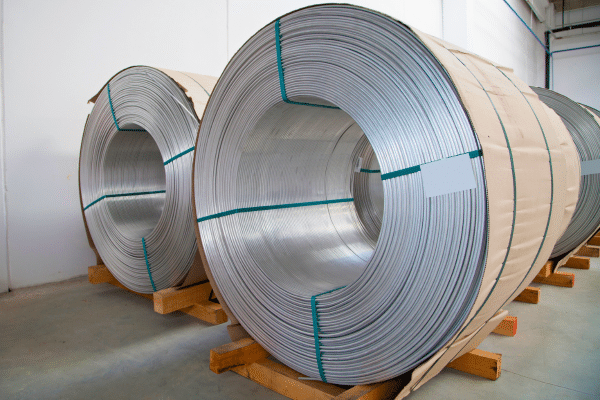
Understanding Aluminum Alloy 5052
Aluminum alloy 5052 is part of the 5000 series. In this series, magnesium is the key part. This alloy has about 2.5% magnesium and a small amount of chromium. These elements provide the alloy with unique features.
The 5052 aluminum alloy is not like many other aluminum alloys. It does not get stronger when heated. Instead, it gets stronger through a method called cold working. This method shapes the alloy at room temperature. By doing this, it changes the structure of the alloy, making it tougher. However, this can also make the alloy a bit less flexible.
Key Characteristics and Properties
Aluminum alloy 5052 is perfect for hard tasks. It has strong protection against corrosion, especially in ocean areas. The magnesium in it helps form a protective layer. This layer prevents harm from saltwater and air.
The magnesium content makes 5052 stronger against fatigue. It can take repeated stress without getting hurt. This feature is crucial for parts that feel vibrations. This includes parts in aircraft and vehicles.
5052 aluminum is easy to weld with regular methods. This makes it easier to create items and gives it more uses. GET A QUOTE
Chemical Composition Breakdown
The special qualities of aluminum alloy 5052 come from its ingredients. The main element added is magnesium, and it plays a key role. When about 2.5% magnesium is added, the alloy becomes stronger. This addition also helps it resist corrosion better and makes it easier to weld.
5052 aluminum has magnesium and small amounts of other key elements. Chromium is usually around 0.25%, which helps boost its resistance to corrosion. It also contains little bits of silicon and manganese. These elements add strength and make the aluminum easier to handle.
The chemical structure of 5052 aluminum can change a bit based on the grade and supplier. Still, the levels of magnesium, chromium, silicon, and manganese usually stay the same. This reliability helps the alloy keep its key features.
How To Choose The Right Temper?
Choosing the right temper for the project is very important when we work with 5052 aluminum. A temper is a special treatment or process done to the alloy. This makes its properties better. The tempers we will see most often for 5052 aluminum come from the H series. These are H32, H34, and H38.
The “H” stands for strain hardening. This means the alloy has been worked in the cold to make it stronger. The numbers (32, 34, 38) show how hard the temper is. A higher number means the temper is tougher and stronger. The “3” in the temper name shows that the stabilization process keeps the alloy’s qualities over time. Picking the right temper depends on the mechanical property requirements of the project.
Practical Applications of Aluminum Alloy 5052
Aluminum alloy 5052 is strong and won’t rust. It is also simple to work with. This mix makes it a favored choice in many fields. We can see it in heavy-duty machines and fragile electronic parts.
Now, let’s explore some key places where 5052 aluminum is very useful. We will review the benefits it offers in each area.
Industrial Uses
In the industrial world, aluminum alloy 5052 is a top project choice. It offers strong protection against rust and good strength. It can handle tough situations well. This makes it suitable for marine uses, such as:
- Boat hulls and parts: This alloy is great at resisting seawater corrosion. It’s ideal for making boat hulls, decks, and other marine parts.
- Chemical tanks and containers: Its strong resistance to chemicals makes it safe for storing and transporting dangerous substances.
- Processing equipment: Aluminum alloy 5052 is used in food processing tools. This is key because keeping things clean and protected from rust is very important.
- Building parts
- Truck and trailer bodies: The alloy is light and does not rust. This makes it a great option for truck and trailer bodies. It also helps save fuel.
- Appliances: The alloy is easy to shape and very strong. This makes it ideal for appliances like refrigerators, washing machines, and dishwashers.
Benefits in Automotive and Aerospace Industries
Aluminum alloy 5052 is not just used in factories. It is also great for tough places like cars and airplanes. This is because it has good weldability and resists rust very well. Its magnesium content gives it a strong strength-to-weight ratio, which makes it a popular choice in these areas.
In the car industry, 5052 aluminum is used in:
- Body panels: They are light and strong, and help cars weigh less. This makes fuel efficiency better.
- Fuel tanks: They resist rust, which keeps the fuel safe during storage and transportation.
- Interior parts: They can have nice, detailed designs inside and still stay strong.
The airplane industry uses 5052 aluminum. This aluminum is light and resists rust. Below are some of its uses:
- Aircraft skin and panels: This alloy is both strong and light. It helps make planes lighter. This change improves how well planes use fuel.
Comparing with other alloys
Aluminum Alloy 5052 is often compared to Alloy 6061 and Alloy 7075 because of its special features. Alloy 5052 is great at resisting corrosion, and we can weld it easily. It also has strong strength against fatigue. In contrast, Alloy 6061 has higher tensile strength and is better for building structures. Alloy 7075 is solid, but it doesn’t fight corrosion as well as Alloy 5052. Knowing these differences can help us pick the best aluminum alloy for our needs. GET A QUOTE
5052 vs 6061
When we look beyond the 5000 series, we find 6061 aluminum. This alloy can be heat treated, which makes it very flexible for different uses. Both 5052 and 6061 have good corrosion resistance and are easy to work with. However, they are quite different when it comes to strength and how they respond to heat treatment.
6061 aluminum gets stronger after heat treatment compared to 5052. This increase in tensile strength makes it a great choice for applications that need extra strength. It is useful for parts in aircraft and bicycle frames.
6061 has good corrosion resistance. However, it is not as high as 5052, which is especially true in places like the ocean. 5052 has a higher magnesium content. This makes it better at fighting against saltwater corrosion.
5052 vs 5082 vs 5083
The 5000 series of aluminum alloys has several types, like aluminum 5052, aluminum 5082, and aluminum 5083. They are similar because each one has magnesium in it. However, each type has slight differences in its chemical makeup. This means they perform differently in various situations.
The table below gives a comparison of these alloys:
Alloy |
Magnesium Content (%) |
Tensile Strength (MPa) |
Typical Applications |
5052 |
2.2 – 2.8 |
228 – 331 |
Marine applications, appliances, general sheet metal work |
5082 |
4.0 – 4.9 |
276 – 393 |
Marine grade aluminum, pressure vessels, structural applications |
5083 |
4.0 – 4.9 |
290 – 414 |
High-strength marine applications, armored plating, cryogenic tanks |
As seen in the table, 5082 and 5083 have more magnesium in them. This means they are stronger than 5052. Because of this strength difference, they are better for some uses.
5052 is good for basic sheet metal work. It works well in places where medium strength is fine. On the other hand, 5082 and 5083 are better options for tougher jobs. You need these grades when you have to hold heavier weights. This includes tasks like building ships and creating pressure vessels.
The Price Of 5052 Aluminum
Aluminum alloy 5052 is popular due to its good resistance to corrosion and strong strength. It has a reasonable price compared to other aluminum alloys. A few things can influence its cost, like market demand, the availability of raw materials, and how it is made. The price can also change depending on the buying quantity and the supplier’s pricing plan. It is important to keep these factors in mind when budgeting for projects that need aluminum alloy 5052. This way, we can ensure that we get the best value for our investing money. GET A QUOTE
Certification of 5052 Aluminum
When purchasing aluminum alloy 5052, ensure to verify its quality by adhering to industry standards. Certifications and specifications can ensure our acquisition.
Groups like the Aluminum Association set and keep standards for aluminum alloys. They ensure the mix and qualities of the alloys meet certain requirements. It is smart to choose suppliers who follow ASTM rules. For example, ASTM B209 covers sheets and plates made from aluminum and aluminum alloys.
Also, look at the Safety Data Sheet (SDS) for the material. This sheet has important details on how to handle and store it. It will also inform us about any risks. This helps us use the material safely and effectively.
Conclusion
Aluminum Alloy 5052 has several benefits. Many industries like to use it. It is very strong and can work in different areas like cars and planes. To get the best results, it’s important to understand its chemical makeup and choose the right temper. When compared to other alloys, 5052 stands out as a strong choice. Its certification proves it is good quality and affordable. Whether we want it for marine use or building structures, Aluminum Alloy 5052 is a good option.
Why Choose Us
Linsy Aluminum as a trusted aluminum supplier in China, we are dedicated to delivering quality and precision with every order. Our position as one of the best aluminum brands speaks to our commitment to excellence, and as a leading aluminum factory in China, we ensure that our products meet the highest industry standards. With advanced technology and strict quality control, we offer reliability and exceptional customer service, providing solutions that are tailored to diverse industrial needs.
Frequently Asked Questions
Why is Aluminum Alloy 5052 preferred for marine applications?
Aluminum alloy 5052 is great at resisting corrosion, especially in marine settings. This is because it has magnesium and chromium (Cr). These elements help form a strong protective layer. This layer keeps seawater and impurities from damaging it.
How does 5052 aluminum compare to other alloys in terms of strength?
5052 aluminum is strong due to its magnesium content. However, it might not be as strong as some heat-treated alloys. Still, its high fatigue strength makes it a great choice for projects that experience regular stress.
Can Aluminum Alloy 5052 be welded, and if so, how?
Aluminum alloy 5052 is easy to weld. You can use regular methods like gas metal arc welding (GMAW) and tungsten inert gas welding (TIG) to join it. The magnesium in the alloy helps with this. You don’t need to heat it before welding. This makes the process quicker and simpler.
What finishes are recommended for Aluminum Alloy 5052?
To make 5052 aluminum stronger against rust, it can have surface finishes like anodizing. Anodizing builds up a thicker oxide layer. This layer protects the alloy and helps it fight corrosion more effectively. You can also use other coatings, like powder coating, to make it stronger and look better.