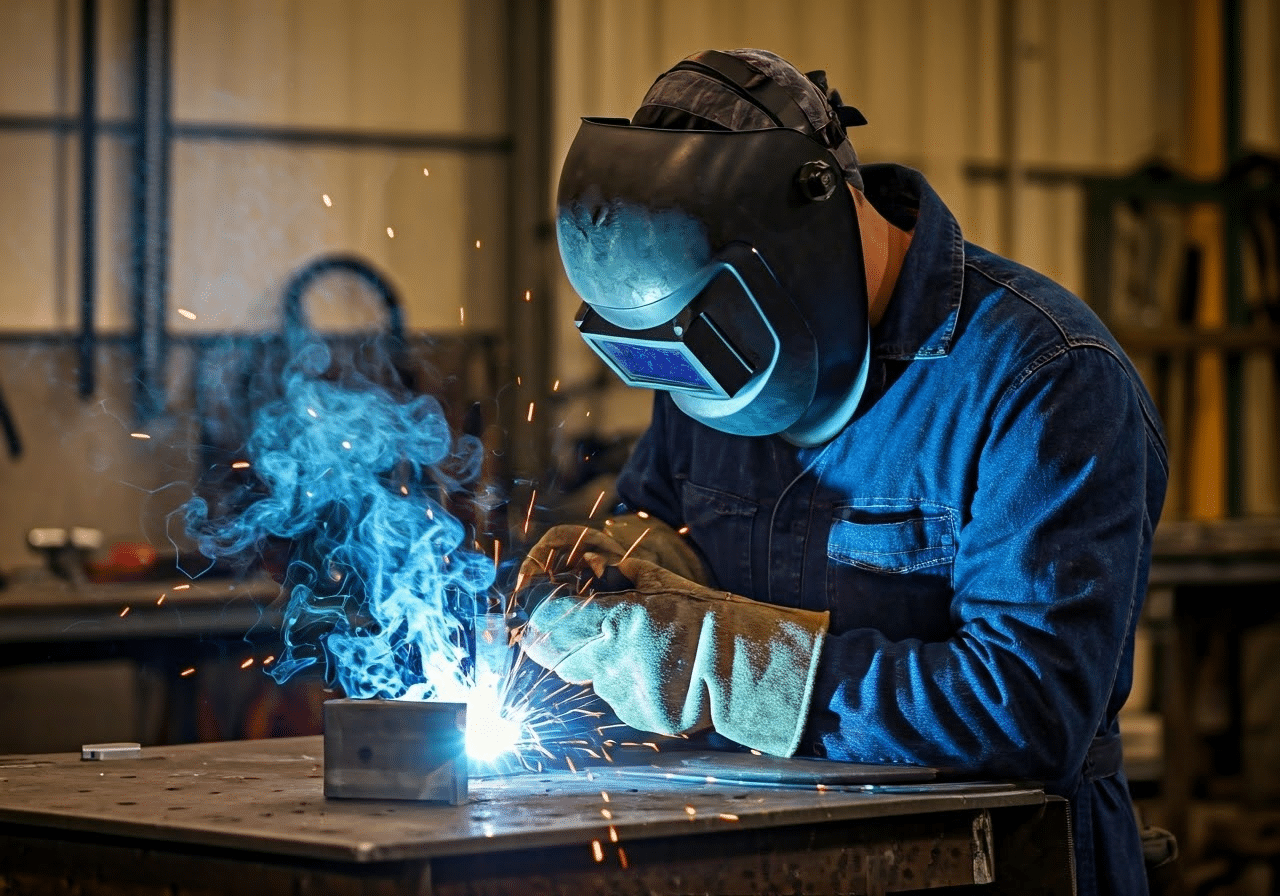
Key Highlights
- Gain insight into the unique challenges of welding 6061 aluminum, including heat treatment and common welding issues.
- Discover why 6061 aluminum is a preferred choice for welding in various industries due to its tensile strength and corrosion resistance.
- Learn about essential equipment and safety measures crucial for successfully welding 6061 aluminium.
- Explore step-by-step guidelines for cleaning, choosing the right welding technique, and testing the strength of 6061 aluminum welds.
- Acquire knowledge on avoiding warping during welding and tips for selecting the appropriate filler material for 6061 welding.
Introduction
Welcome to the Expert 6061 Aluminum Welding Guide, a comprehensive resource for mastering the art of welding this versatile alloy. This guide is designed to equip you with the knowledge and skills to tackle the unique challenges of welding 6061 aluminum. Let’s delve into the intricacies of welding this material, exploring the welding techniques, common challenges, and why 6061 aluminum stands out as a preferred choice for various industries. Let’s begin your journey to becoming a proficient 6061 aluminum welder.
Understanding 6061 Aluminum and Its Welding Challenges

6061 aluminum, a popular alloy, offers excellent weldability due to its magnesium and silicon content. However, its high strength can lead to cracking if not welded correctly. Challenges such as hot cracking and porosity are common during welding. Understanding the material properties and suitable welding techniques is crucial for successful welds. Balancing heat input and filler metal selection is essential to overcome the unique challenges presented by 6061 aluminum. Advanced knowledge of NLP terms can aid in optimizing welding parameters for this alloy.
The Basics of 6061 Aluminum
6061 aluminum is a versatile alloy known for its excellent strength-to-weight ratio and corrosion resistance. It belongs to the 6xxx series of aluminum alloys and is commonly used in various industries due to its weldability and good mechanical properties. This alloy can be easily welded using different techniques like gas tungsten arc welding (GTAW) or gas metal arc welding (GMAW), making it a popular choice for fabricators and welders alike. Understanding the basics of 6061 aluminum is crucial for successful welding projects.
Common Welding Challenges with 6061 Aluminum
6061 aluminum welding presents some common challenges. One issue is its high crack sensitivity, requiring precise heat control during the welding process. Another challenge is its susceptibility to hot cracking, especially in thick sections. Additionally, 6061 aluminum has a high thermal conductivity that can lead to overheating. These challenges demand expertise in managing heat input, selecting appropriate filler metals, and implementing proper welding techniques to ensure successful welds on 6061 aluminum.
Why Choose 6061 Aluminum for Welding?
6061 aluminum is favored for welding due to its high strength, excellent corrosion resistance, and good machinability post-welding. Its versatility and durability make it ideal for various applications in aerospace, marine, and structural projects.
Welding Techniques for 6061 Aluminum
When welding 6061 aluminum, various techniques can be employed to ensure a successful weld. Common methods include gas metal arc welding (GMAW), gas tungsten arc welding (GTAW), and laser beam welding. Each technique offers unique advantages depending on the specific requirements of the project. GMAW, also known as MIG welding, is popular due to its ease of use and high welding speed. GTAW, or TIG welding, provides precise control over the welding process, making it ideal for intricate welds. Laser beam welding offers high welding speeds and minimal heat input, suitable for thin materials.
Preparing for Welding 6061 Aluminum: A Beginner’s Guide
Essential gear like a welding machine, filler metals, and personal protective equipment are crucial for welding 6061 aluminum. Safety measures such as proper ventilation and protective clothing must be observed. Understanding the metal’s properties, like its excellent weldability and strength, is fundamental. Prepping the material by cleaning the surface from any contaminants ensures a successful weld. Taking precautions to prevent overheating and selecting the appropriate welding technique for the task are essential steps for beginners entering the world of 6061 aluminum welding.
Essential Equipment and Resources
To weld 6061 aluminum effectively, ensure you have a TIG or MIG welder with adjustable settings suitable for aluminum welding, a spool gun for MIG welding, aluminum filler metal matching the alloy, appropriate shielding gas such as argon, a wire brush for cleaning, and safety gear like gloves and a welding helmet. Additionally, having a wire cutter, tungsten grinder, and a dedicated work area with proper ventilation is crucial for a successful welding operation. These resources are indispensable for achieving quality welds on 6061 aluminum.
Safety Measures and Precautions
Remember to prioritize safety when welding 6061 aluminum. Wear appropriate personal protective equipment (PPE) such as gloves, helmet, and protective clothing. Ensure proper ventilation in the workspace to prevent exposure to harmful fumes. Maintain a clean and organized work area to reduce the risk of accidents. Avoid welding in damp conditions to prevent electric shock. Familiarize yourself with emergency procedures and have a fire extinguisher nearby. Prioritize safety to create a secure welding environment. Stay safe and weld responsibly.
Step-by-Step Guide to Welding 6061 Aluminum
The initial step is cleaning and preparing the metal. Next, the right welding technique must be selected based on the metal thickness. For 6061 aluminum, gas tungsten arc welding (GTAW) is commonly used. Adequate penetration is crucial. The process requires shielding gas such as argon. Following this, apply the filler metal carefully to ensure a strong weld. Post-weld heat treatment may be necessary for improved temper and corrosion resistance.
Step 1: Cleaning and Preparing the Metal
Ensure meticulous cleaning of the 6061 aluminum surface using a degreasing solvent to eliminate any contaminants. Utilize a stainless steel brush for stubborn contaminants. Preparing the metal involves removing any oxide layers using a stainless steel wire brush or a dedicated aluminum brush. This crucial step ensures optimal weld quality by promoting strong adhesion between the base metal and the filler material.
Step 2: Choosing the Right Welding Technique
Selecting the appropriate welding technique is critical for welding 6061 aluminum. Processes such as gas tungsten arc welding (GTAW) and gas metal arc welding (GMAW) are commonly used for this alloy. GTAW, also known as TIG welding, offers precise control and high-quality welds suitable for thinner materials. On the other hand, GMAW, or MIG welding, provides faster production speeds and can handle thicker sections efficiently. Understanding the project requirements and material thickness will guide your choice of welding process for optimal results.
Conclusion
Ensuring proper understanding of 6061 aluminum welding is crucial to mastering this process. By comprehending the unique challenges, selecting suitable welding techniques, and following meticulous steps, successful outcomes can be achieved. Remember, thorough preparation, including equipment readiness and safety precautions, is paramount. Embracing the intricacies of 6061 aluminum welding opens up a world of possibilities across various industries. With dedication and practice, mastering the art of welding this versatile material can lead to exceptional results.
Frequently Asked Questions
What is the best welding method for 6061 aluminum?
The best welding method for 6061 aluminum is Tungsten Inert Gas (TIG) welding. TIG welding offers precise control over the heat input, ensuring a clean and strong weld on this alloy.
Can I weld 6061 aluminum without pre-heating?
Welding 6061 aluminum without pre-heating is possible but not recommended. Pre-heating helps prevent cracking and ensures better fusion. Without pre-heating, the weld may be weaker or more prone to defects.
How do I avoid warping when welding 6061 aluminum?
To prevent warping when welding 6061 aluminum, preheat the material uniformly, use minimal heat input, employ backstep welding technique, and utilize fixtures to secure the workpiece. Controlling heat distribution and managing cooling rates are crucial in minimizing distortion.
Tips for selecting filler material for 6061 welding?
Selecting the right filler material for welding 6061 aluminum is crucial. Consider factors like alloy compatibility, joint design, and desired weld characteristics. Common choices include ER4043 and ER5356. Consult with experts or reference material to ensure optimal results.
How do I test the strength of a 6061 aluminum weld?
To test the strength of a 6061 aluminum weld, perform destructive testing methods like tension and bend tests. Non-destructive options include ultrasonic testing or radiography to assess weld quality without compromising the material integrity.