Key Highlights
-
6101 aluminum is lauded for its impressive electrical conductivity, making it a top choice for electrical applications.
-
This alloy strikes an advantageous balance between moderate strength and impressive corrosion resistance.
-
When compared to copper, 6101 aluminum boasts a lighter weight while maintaining comparable conductivity.
-
The adaptability of 6101 aluminum is evident in its suitability for various manufacturing processes, including extrusion, machining, and welding.
-
From bus bars in electrical systems to components in heat exchangers, 6101 aluminum proves its versatility across a range of industries.
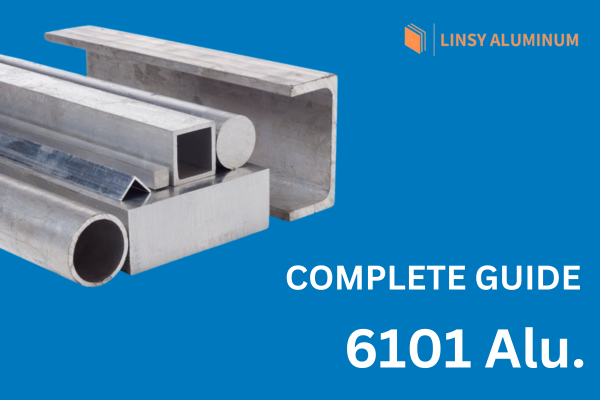
Introduction
In the world of metals, 6101 aluminum stands out as a highly sought-after material, especially when it comes to electrical applications. Renowned for its excellent electrical conductivity, this remarkable alloy facilitates the efficient flow of electrical current. Moreover, 6101 aluminum showcases its resilience through remarkable corrosion resistance, ensuring longevity even in demanding environments. Complementing these benefits is its moderate strength, providing the necessary structural integrity for diverse applications.
Definition and Composition of 6101 Aluminum
6101 aluminum belongs to the 6000 series of aluminum alloys, known for their heat-treatable nature and enhanced strength. What sets 6101 apart within this series is its exceptional electrical conductivity, surpassing other alloys in its class. This makes it particularly well-suited for applications where electrical current flow is paramount.
The remarkable properties of this alloy stem from its precise chemical composition. While aluminum forms the base, carefully measured additions of silicon (Si), iron (Fe), manganese (Mn), and chromium (Cr) contribute to its unique characteristics. These alloying elements work synergistically, enhancing electrical conductivity and other desirable traits like corrosion resistance and machinability.
Key Properties of 6101 Aluminum Alloy
-
Its density (2.7 g/cm³) keeps it light, perfect for things like bus bars that need to stay manageable.
-
The melting point (~600–650°C) means it can handle decent heat before softening, though it’s not for extreme conditions.
-
Thermal conductivity (210–225 W/m·K) is high, so it moves heat away fast, and its electrical conductivity (55–60% IACS) is a standout—better than most aluminum alloys—which is why it’s used in power lines.
-
Finally, tensile strength (~200–220 MPa) is solid but not super high, so it’s strong enough for conductors, not heavy structures. In short, 6101 is light, conductive, and practical—built for power, not brute force!
Property |
Value |
Notes |
---|---|---|
Density |
2.7 g/cm³ |
Lightweight, typical for aluminum. |
Melting Point |
~600–650°C (1,112–1,202°F) |
Range depends on alloy mix. |
Thermal Conductivity |
210–225 W/m·K (T6 temper) |
Excellent heat dissipation. |
Electrical Conductivity |
55–60% IACS (T6 temper) |
High for aluminum, great for conductors. |
Specific Heat Capacity |
0.897 J/g·K |
Energy needed to heat it up. |
Coefficient of Thermal Expansion |
23.4 µm/m·K (20–100°C) |
Moderate expansion with heat. |
Tensile Strength |
~200–220 MPa (T6) |
Moderate, depends on temper. |
Applications of 6101 Aluminum Alloy
The unique properties of 6101 aluminum make it a prime candidate for various electrical applications. Its high electrical conductivity and moderate strength make it an ideal choice for use in bus bars, which are critical components in electrical distribution systems responsible for carrying high currents. Other notable electrical applications include components for transformers, electrical conductors, and heat sinks.
Beyond electrical applications, 6101 aluminum’s good formability allows for its use in various industries. It can be readily shaped into intricate designs, making it suitable for manufacturing products like heat exchangers, automotive components, and architectural elements. Its ability to be extruded with ease further enhances its versatility, enabling the creation of complex profiles with tight tolerances.
Pros and Cons of 6101 Aluminum Alloy
Pros |
Cons |
---|---|
High electrical conductivity (~55–60% IACS) |
Lower strength (~200 MPa in T6) |
Excellent corrosion resistance |
Not ideal for complex extrusions |
Good formability and weldability |
Limited high-temperature performance |
Lightweight (2.7 g/cm³) |
Less versatile than 6061 or 6063 |
Cost-effective for electrical uses |
Lower fatigue resistance |
Undoubtedly, 6101 aluminum boasts several advantages. With its exceptional electrical conductivity, it outperforms numerous other alloys in this domain. Notably, minor chemistry changes contribute to its remarkably high conductivity, making it a preferred choice for electrical applications. Moreover, its combination of moderate-to-high strength and lightweight characteristics makes it an ideal material for a wide range of uses.
However, like any other material, 6101 aluminum also has its limitations. While its strength is commendable, it is essential to note that it might not be the ideal choice for applications demanding exceptionally high tensile strength. Opting for alternative aluminum alloys specifically engineered for superior strength would be more suitable in such scenarios. However, its many positive attributes make it an excellent overall choice in numerous situations.
6101 Aluminum Alloy vs. Other Alloys
While aluminum 6101 is well-regarded among aluminum alloys, exploring its characteristics in comparison to other alloys provides a comprehensive understanding of its specific strengths. This comparative analysis helps determine the most suitable alloy for particular applications based on factors like conductivity, strength, and cost-effectiveness.
In the following sections, we will juxtapose 6101 aluminum with its close counterparts—6061 and 1350 aluminum—to clearly highlight their differences. This exploration assists in making informed decisions when selecting the optimal aluminum alloy for specific project requirements.
6101 vs. 6061 vs. 6063 Aluminum Alloy
Property/Feature |
6101 Aluminum Alloy |
6061 Aluminum Alloy |
6063 Aluminum Alloy |
---|---|---|---|
Main Composition |
Al + 0.6% Mg + 0.5% Si |
Al + 1% Mg + 0.6% Si |
Al + 0.4% Mg + 0.7% Si |
Tensile Strength |
Moderate (e.g., 200 MPa in T6) |
Moderate-High (e.g., 310 MPa in T6) |
Low-moderate (e.g., 241 MPa in T6) |
Electrical Conductivity |
High (55–60% IACS) |
Moderate (40–45% IACS) |
Moderate-High (50–55% IACS) |
Extrudability |
Moderate (simple shapes) |
Good (less complex shapes) |
Excellent (smooth, complex shapes) |
Corrosion Resistance |
Excellent |
Very Good |
Excellent |
Weldability |
Very Good |
Excellent |
Very Good |
Typical Use |
Bus bars, electrical conductors |
Structural parts, frames |
Architectural trim, window frames |
6101, 6061, and 6063 are all 6000-series aluminum alloys, but they’re suited for different jobs.
-
6101 Aluminum is the electrical whiz—its high conductivity (up to 60% IACS) makes it perfect for power lines or bus bars, though it’s not super strong or great for fancy shapes.
-
6061 Aluminum is the all-rounder, stronger (310 MPa), and versatile material used in everything from bike frames to boat parts; it’s weldable and tough but not the best for intricate designs.
-
6063 Aluminum is the extrusion star, shaping easily into smooth, pretty profiles like window frames. It has decent strength and top-notch corrosion resistance. All three fight rust well and weld nicely, but pick 6101 for electrical work, 6061 for sturdy builds, and 6063 for sleek looks!
When to choose 6101 Aluminum
Factor |
Why It Matters |
Choose 6101 If… |
---|---|---|
Electrical Conductivity |
High conductivity for power transfer. |
You need it for bus bars or conductors (55–60% IACS). |
Strength Needs |
Moderate strength, not for heavy loads. |
Low-to-moderate strength (~200 MPa) is enough. |
Corrosion Resistance |
Excellent rust resistance. |
It’s in mild or semi-outdoor conditions. |
Weldability |
Easy to weld with strong joints. |
Your project involves welding. |
Shape Complexity |
Best for simple forms, not intricate profiles. |
You only need basic shapes, not complex extrusions. |
Cost Efficiency |
Affordable for electrical applications. |
Budget matters and conductivity is key. |
Weight |
Lightweight material at 2.7 g/cm³. |
You need a light alloy for the job. |
Applications |
|
You use it in Electrical components |
Heads-Up: If your project demands high strength, complex shapes, or extreme heat resistance, consider alloys like 6061, 6063, or 2219 instead.
Conclusion
6101 Aluminum is a versatile alloy with various applications, especially in electrical and structural fields. Its unique properties make it a preferred choice for various industries. Understanding the composition, pros, and cons of 6101 Aluminum can help you make informed decisions about its usage. This guide provides comprehensive insights, whether considering its conductivity or comparing it to other alloys. If you’re looking to source 6101 Aluminum, reach out for quotes to start your next project seamlessly.
Why Choose Linsy Aluminum
As one of the leading aluminum brands and a top supplier in China, Linsy Aluminum emphasizes quality and reliability in all its products. Our advanced aluminum factory in China manufactures high-performance aluminum alloys that satisfy the toughest industry requirements. Dedicated to excellence, we provide precision, durability, and tailored options to accommodate your specific project needs, establishing us as a trusted partner for businesses globally searching for exceptional aluminum solutions. GET A QUOTE
Frequently Asked Questions
What makes 6101 aluminum ideal for electrical applications?
6101 aluminum is a prime choice for electrical applications due to its excellent electrical conductivity, which ensures efficient current flow. Its good corrosion resistance ensures longevity, while moderate strength provides structural integrity. Furthermore, its thermal conductivity aids in heat dissipation, which is crucial in electrical systems.
How does 6101 compare to other aluminum alloys in terms of conductivity?
6101 aluminum boasts high electrical conductivity, exceeding many aluminum alloys. While not as conductive as specialized alloys like 1350, it surpasses others like 6061. Compared to copper, it offers comparable conductivity with added benefits of lower weight and cost, making it a compelling choice where both conductivity and cost are a factor.
Can 6101 aluminum be used in structural applications?
While 6101 aluminum possesses moderate strength and good formability, it may not be the primary choice for high-stress structural applications. Its strength, enhanced through heat treatment, is suitable for applications with moderate structural demands but might not be ideal when greater strength is paramount.
What are the common finishes available for 6101 aluminum products?
6101 aluminum, inherently endowed with respectable corrosion resistance, benefits further from various finishes that enhance its surface protection and aesthetic appeal. Common finishes include anodizing, which provides a durable oxide layer for enhanced protection, and powder coating, which offers a wide range of colors and textures.
How to properly maintain and care for 6101 aluminum?
Thanks to its inherent corrosion resistance, 6101 aluminum requires minimal maintenance. Regular cleaning with mild soap and water is usually sufficient to preserve its appearance and conductivity. However, applying a protective wax coating in harsh environments can further enhance its corrosion resistance.