Key Highlights
- Aluminium alloy 2014 is renowned for its high strength-to-weight ratio.
- This alloy exhibits good machinability, making it suitable for detailed fabrication.
- It’s a top choice for demanding applications, such as aerospace structures and heavy-duty vehicles.
- Corrosion resistance is a key consideration, often addressed with protective coatings like Alclad or anodizing.
- 2014 aluminium alloy is a staple in high-performance engineering due to its excellent mechanical properties.
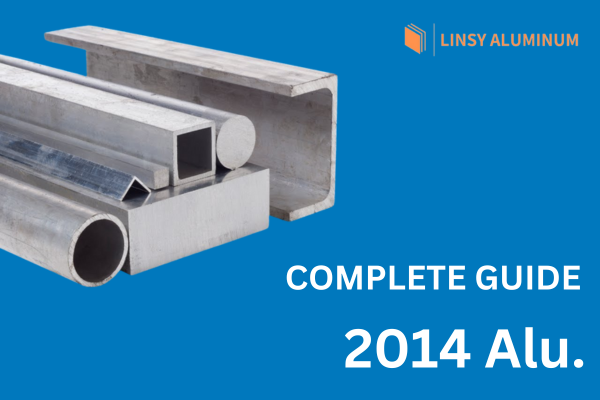
Introduction
Aluminium alloy 2014, also known as 2014 Aluminum Alloy, is a high-strength material widely used in B2B industries such as aerospace and automotive. Its exceptional combination of strength and mechanical properties makes it a valuable choice for applications where weight-saving is essential without compromising structural integrity. In this blog, we will explore the composition, properties, applications, and benefits of 2014 Aluminum Alloy for manufacturing, highlighting why it’s worth exploring in detail.
What is Aluminium Alloy 2014?
Aluminium alloy 2014 is a high-strength material primarily composed of copper. It offers excellent machinability and weldability, making it ideal for structural applications in the aerospace and transportation industries. With good corrosion resistance and moderate toughness, it’s a popular choice for various engineering projects.
Overview of Its Chemical Composition
The key to understanding the impressive properties of the 2014 aluminium alloy lies in its chemical composition. Copper plays the most significant role, with content between 3.9% and 5%, bolstering the alloy’s strength.
Magnesium, typically 0.2% to 0.8%, is another essential element contributing to the alloy’s heat-treatable nature. Silicon, 0.5% to 1.2%, further enhances its casting characteristics and helps control the material’s grain structure.
Lastly, manganese, with a typical content of 0.2% to 1.2%, is added to improve the alloy’s strength and corrosion resistance. This carefully balanced composition gives aluminium alloy 2014 exceptional strength, workability, and suitability for demanding applications.
Element |
Content-Range |
Role |
---|---|---|
Copper |
3.9% – 5% |
Primary alloying element for high-strength |
Magnesium |
0.2% – 0.8% |
Contributes to heat-treatable nature for enhanced durability |
Silicon |
0.5% – 1.2% |
Enhances casting characteristics and controls the grain structure |
Manganese |
0.2% – 1.2% |
Improves strength and corrosion resistance |
Highlighted Key Properties:
- High Strength
- Good Machinability
- Moderate Corrosion Resistance
Aluminium alloy 2014 is suitable for heavy-duty applications and is heat-treatable for enhanced durability.
Understanding Its Key Physical and Mechanical Properties
Aluminium alloy 2014 boasts a remarkable tensile strength of up to 427 MPa, placing it among the strongest in the aluminium alloy family. This robust tensile strength allows it to withstand significant pulling forces before deformation.
Property |
Value |
---|---|
Tensile Strength |
427 MPa |
Yield Strength |
290 MPa |
Thermal Conductivity |
192 W/mK |
Furthermore, its yield strength, at which permanent deformation occurs, measures around 290 MPa, demonstrating its ability to handle substantial stress. Aside from strength, its thermal conductivity, at 192 W/mK, makes it efficient in heat dissipation, a crucial factor in various applications.
Its impressive ultimate tensile strength allows it to resist breaking under extreme stress, making it a top choice for heavy-duty applications across industries.
Benefits and Limitations of 2014 Aluminum Alloy
Advantages:
- High strength-to-weight ratio
- Excellent machinability for precision parts
Drawbacks:
- Lower corrosion resistance compared to other alloys
- Not ideal for welding
2014 aluminum alloy offers exceptional benefits, including high strength, good machinability, and excellent corrosion resistance. These properties make it ideal for structural applications in aerospace and military vehicles. However, its limitations lie in lower toughness compared to other alloys like 7075 and 2024. While the 2014 alloy showcases impressive electrical conductivity and thermal properties, it may not be suitable for applications requiring the highest tensile strength available among aluminium alloys. Nonetheless, its versatility and moderate hardness make it a valuable choice in various industries.
Key Applications and Uses of Aluminium Alloy 2014
Aluminium alloy 2014 finds its niche in high-stress applications across different sectors. Its exceptional strength-to-weight ratio makes it ideal for components where weight reduction is critical without sacrificing structural integrity.
Key uses include aircraft structures, military vehicles, and heavy-duty machinery. It’s found in the aerospace industry’s structural components like wing spars, fuselage parts, and landing gear, underscoring its reliability under demanding conditions.
Aerospace Components Utilizing Alloy 2014
In the aerospace industry, where strong and light materials are necessary, 2014 aluminium alloy forgings are crucial. This alloy can handle the extreme stresses of flight while being lightweight, making it essential for important aircraft parts.
These forgings are commonly used to make structural parts like wing spars, ribs, and fuselage frames, which must be strong but light. The great fatigue resistance of the 2014 aluminium alloy ensures that these parts can handle the stresses of flight, ensuring long-lasting performance and safety.
Additionally, the alloy is easy to machine, making it good for creating complex shapes needed in aerospace designs. This, along with its high strength, makes it a top choice for making landing gear components that need to withstand the impact forces during takeoff and landing.
Other Industrial Applications
Beyond its dominance in aerospace, 2014 aluminium alloy finds widespread use in other demanding industries such as automotive, military, machinery, and structural engineering. Its impressive strength-to-weight ratio is highly valued in the automotive sector, particularly in producing high-performance vehicles and heavy-duty trucks.
Military vehicles also benefit significantly from this alloy’s properties. Its strength and lightweight make it ideal for structural applications and armour plating, ensuring robust performance in challenging environments.
In machinery and structural engineering, the 2014 aluminium alloy is utilized for its strength and durability. Its properties make it suitable for various applications where a balance of strength and lightweight is required. Additionally, its moderately high electrical conductivity makes it suitable for certain electrical components and connectors.
Comparison: 2014 Aluminum Alloy vs Other Alloys
2014 aluminium alloy offers good machinability and corrosion resistance but falls short in strength compared to 7075 alloys. While 2024 and 6061 alloys provide higher tensile strength, they are less corrosion-resistant. 2014 alloy is preferred for its suitability in structural applications, while 7075 is favoured for its high strength. Each alloy has distinct mechanical and physical properties, catering to specific aerospace and automotive manufacturing needs.
2014 Vs. 2024 Vs. 6061 Vs. 7075 Aluminum
Feature |
2014 Aluminum |
2024 Aluminum |
6061 Aluminum |
7075 Aluminum |
---|---|---|---|---|
Main Makeup |
Al + 4.4% Cu + Si |
Al + 4.4% Cu + 1.5% Mg |
Al + 1% Mg + 0.6% Si |
Al + 5.6% Zn + 2.5% Mg |
Strength |
High (~420–480 MPa, T6) |
Very High (~470 MPa, T3) |
Moderate (~310 MPa, T6) |
Extremely High (~570 MPa, T6) |
Corrosion Resistance |
Poor (needs coating) |
Poor (needs cladding) |
Very Good |
Moderate (better than 2000-series) |
Weldability |
Poor (prone to cracking) |
Poor (prone to cracking) |
Excellent |
Poor (not recommended) |
Machinability |
Excellent |
Good |
Good |
Good |
Typical Use |
Aircraft parts, wheels |
Aircraft skins, structures |
Bike frames, boats |
Military, aircraft frames |
In summary, the 2014 aluminium alloy offers good machinability and corrosion resistance, suitable for structural applications. 2024 provides high strength and is favoured for aerospace usage. 6061 balances strength and weldability, ideal for various applications. 7075 stands out for its high hardness and strength properties, commonly used in military vehicles. Each alloy has distinct characteristics that suit specific industries and applications. The choice depends on the required properties and intended use.
Tips to Choose the Right Alloy
Picking the right alloy from 2014, 2024, 6061, and 7075 depends on what your project needs. Here’s how to decide:
- Need Super High Strength?
Go for 7075—it’s the strongest (570 MPa) and perfect for heavy-duty jobs like military gear or aircraft frames. But it’s hard to weld and needs rust protection. - Working on Aircraft Parts?
Choose 2014 or 2024. Both are strong (420–480 MPa for 2014, 470 MPa for 2024) and great for aerospace—2014 for wheels or fittings, 2024 for skins or structures. They’re awesome for machining but rust easily, so add a coating. - Need to Weld a Lot?
Pick 6061—it welds the best and fights rust well. It’s not as strong (310 MPa), but it’s perfect for bike frames, boats, or pipes where joining and weather resistance matter. - Dealing with Harsh Weather?
Stick with 6061 for its great corrosion resistance—it holds up outdoors without much help. 7075 is okay too, but 2014 and 2024 will need coatings to avoid rust. - Machining Small Parts?
Go with 2014—it’s the easiest to cut and shape, making it ideal for detailed parts like screws or fittings. 2024, 6061, and 7075 are good but not as smooth.
Match the alloy to your needs: 7075 for max strength, 2014 or 2024 for aircraft and machining, and 6061 for welding and rust resistance. Check your project’s strength, weather, and workability needs to pick the right alloy!
Conclusion
Aluminium Alloy 2014 is a versatile material known for its unique properties and wide range of applications, especially in the aerospace and industrial sectors. Understanding its chemical composition, physical and mechanical attributes, as well as its benefits and limitations, is crucial for leveraging its full potential. When comparing it to other alloys like 2024, 6061, and 7075, knowing which alloy suits your specific needs is key. Whether you’re in aerospace or other industries, the choice of aluminium alloy can significantly impact the performance of your components. Dive deeper into the world of Aluminium Alloy 2014 to discover its exceptional qualities and find the perfect fit for your projects.
Why Choose Linsy Aluminum
As one of the leading aluminum brands and a top supplier in China, Linsy Aluminum emphasizes quality and reliability in all its products. Our advanced aluminum factory in China manufactures high-performance aluminum alloys that satisfy the toughest industry requirements. Dedicated to excellence, we provide precision, durability, and tailored options to accommodate your specific project needs, establishing us as a trusted partner for businesses globally searching for exceptional aluminum solutions. GET A QUOTE
Frequently Asked Questions
What is the difference between 2014 and 2024 aluminum?
Both alloys offer high tensile strength, but 2024 aluminum exhibits slightly better weldability and formability. However, 2014 aluminum surpasses 2024 in terms of yield strength and boasts higher thermal conductivity, making it more suitable for applications demanding higher strength and heat dissipation.
How Does Alloy 2014 Compare to Other Aluminium Alloys in Terms of Strength?
Aluminium alloy 2014 is among the high-strength aluminum alloys, exhibiting impressive tensile strength and yield strength. While not as strong as 7075, its higher ultimate tensile strength surpasses 6061 and rivals 2024, making it a strong choice for demanding applications.
What Makes Aluminium Alloy 2014 Suitable for Aerospace Applications?
The high strength-to-weight ratio, excellent mechanical properties, and favorable thermal conductivity make aluminium alloy 2014 ideal for aerospace applications demanding lightweight yet strong materials capable of withstanding flight stresses.
Can Aluminium Alloy 2014 Be Welded Easily?
While weldable, aluminium alloy 2014 requires controlled heat treatment and specialized techniques due to its susceptibility to cracking during welding. Its thermal conductivity and potential changes in mechanical properties near welds need careful consideration.
What Are the Main Challenges When Working with Alloy 2014?
The primary challenges lie in its lower corrosion resistance compared to other aluminium alloys, necessitating protective coatings. While exhibiting good machinability, its heat treatment requires careful control to achieve desired mechanical properties without compromising its integrity.
Are There Any Specific Heat Treatments Recommended for Alloy 2014?
Solution heat treatment followed by artificial aging, commonly known as T6 temper, is recommended to achieve the desired high strength and optimal mechanical properties. This heat treatment process enhances its performance capabilities in demanding applications.