Key Highlights
- 2618 aluminum alloy is known for its high strength, especially at elevated temperatures, making it perfect for demanding applications.
- This alloy is a preferred choice for pistons, engine parts, and structural components in the aerospace and motorsports industries.
- Notable for its excellent mechanical properties, 2618 aluminum showcases good machinability in heat-treated conditions.
- With copper and magnesium as its primary alloying elements, this aluminum grade offers remarkable corrosion resistance, further expanding its suitability for diverse operating conditions.
- Specific heat treatment processes, including solution heat treatment and aging, can further enhance the alloy’s strength.
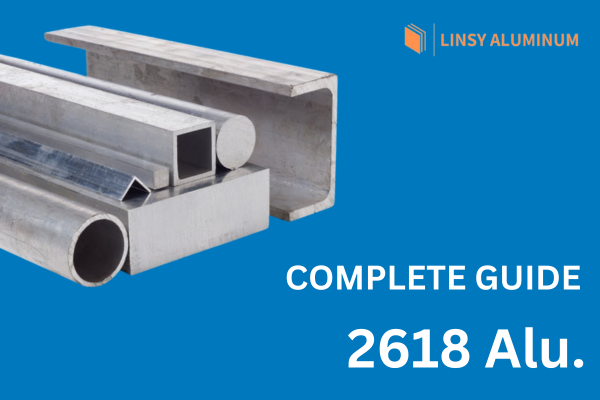
Introduction
Widely recognized for its exceptional strength-to-weight ratio and impressive high-temperature performance, 2618 Aluminum Alloy is prominent in high-performance materials, particularly in demanding industries such as aerospace and motorsports.
This article aims to explore the intricacies of this remarkable alloy. We will cover its properties, applications, and advantages, as well as shed light on the benefits of 2618 aluminum alloy for high-temperature use and appropriate heat treatment methods to achieve desired mechanical properties. Further, we’ll examine 2618 aluminum forgings – a popular form for this alloy, highlighting its significance in various industrial sectors.
What is 2618 Aluminum Alloy
2618 aluminum alloy belongs to the heat-treatable wrought aluminum alloy family, known for its exceptional strength, particularly at elevated temperatures. Its remarkable combination of strength, toughness, and machinability sets it apart, making it a top choice for demanding applications. The alloy’s composition, primarily aluminum, copper, and magnesium, contributes to its impressive performance characteristics.
This specific blend of elements allows 2618 aluminum to excel in scenarios where maintaining structural integrity under stress and at high temperatures is critical. Whether it’s an aircraft engine’s demanding environment or motorsports’s high-performance needs, 2618 aluminum alloy consistently delivers.
Overview of Its Chemical Composition
The distinctive characteristics of the 2618 aluminum alloy can be linked to its unique chemical composition. Here is a breakdown of the key alloying elements that contribute to its strength and functionality:
Element |
Composition Percentage |
Role |
---|---|---|
Aluminum |
90% |
Base material |
Copper |
2-3% |
Enhances strength, especially after heat treatment |
Magnesium |
1.2-1.8% |
Collaborates with copper to further strengthen the alloy |
Nickel |
1.2-1.8% |
Improves performance at high temperatures and durability |
By carefully incorporating these alloying elements during production, the manufacturing process guarantees that the alloy satisfies the rigorous standards required by industries like aerospace, where material durability and performance are critical.
Key Physical and Mechanical Properties of 2618 Aluminum Alloy
Property |
Value |
What It Means |
---|---|---|
Density |
2.75 g/cm³ |
Pretty light for a strong metal. |
Melting Point |
~550–640°C (1,022–1,184°F) |
Stays solid until really hot. |
Tensile Strength |
~420–450 MPa (T6) |
Super strong for heavy jobs. |
Yield Strength |
~350–380 MPa (T6) |
Takes a lot before it bends. |
Elongation |
~5–10% |
Not very stretchy, but tough. |
Hardness |
~120–130 HB (Brinell, T6) |
Hard, doesn’t scratch easily. |
Thermal Conductivity |
~140–155 W/m·K |
Moves heat pretty well. |
Fatigue Strength |
~150–180 MPa |
Handles repeated stress like a champ. |
2618 Aluminum Alloy is a tough metal that’s great for high-stress jobs.
- It’s light (2.75 g/cm³), so it doesn’t add much weight, which is awesome for airplane parts.
- It melts at around 550–640°C, meaning it can handle hot conditions—like in engines—without turning to mush.
- It’s really strong (420–450 MPa), so it can take a lot of force, and its yield strength (350–380 MPa) means it won’t bend easily. It’s not super stretchy (5–10%), but that’s okay because it’s built for toughness, not bending.
- It’s hard (120–130 HB), so it won’t scratch up fast. It’s great with repeated stress (150–180 MPa), making it perfect for parts that get used a lot, like pistons.
- Plus, it moves heat well (140–155 W/m·K), which helps in hot environments. 2618 is a strong, heat-loving metal for serious projects!
Benefits and Limitations of 2618 Aluminum Alloy
Benefits |
Limitations |
---|---|
High strength at elevated temperatures |
Lower corrosion resistance compared to other alloys |
Good fatigue resistance |
Higher cost than general-purpose alloys |
Decent corrosion resistance (with treatment) |
Susceptibility to stress corrosion cracking (SCC) |
Good machinability |
Limited cold formability |
Weldable (with specific techniques) |
Slightly denser than some aluminum alloys |
Heat treatable for enhanced properties |
Complex processing (heat treatment required) |
Practical Applications of 2618 Aluminum Alloy
Highly valued in aerospace, 2618 aluminum alloy has extensive practical applications. Its high load-bearing capacity and excellent mechanical properties make it ideal for manufacturing pistons and aluminum forgings. Known for its corrosion resistance and heat treatment capabilities, this alloy, with its high strength, is often the top choice for applications requiring durability under extreme conditions. Whether in the form of round bars or forgings, the specifications of 2618 aluminum alloy meet the stringent requirements of industries where reliability is non-negotiable.
Aerospace and Motorsports
In the tough aerospace world, 2618 aluminum is crucial. Due to its strong yet light properties, it’s commonly used to make aircraft parts like engines, fuselages, and wings.
This aluminum maintains its strength even at high heat, which is vital for aircraft engines. Parts like pistons endure heat and pressure, benefiting from this strong alloy. It ensures engines work well even under tough conditions.
Likewise, the fast motorsports industry likes 2618 aluminum for its strength and toughness. Racing engine pistons often use this alloy due to its high-temperature resistance. This helps components last in the challenging motorsports setting.
Comparison: 2618 Aluminum Alloy vs Other Alloys
While 2618 aluminum alloy excels in many ways, comparing it to other aluminum alloys is crucial for selecting the right material for specific needs. Each aluminum alloy presents unique characteristics for different situations, depending on strength, formability, corrosion resistance, and cost-effectiveness.
Examining these differences empowers engineers and manufacturers to make informed decisions based on application-specific requirements, optimizing material selection for optimal results.
2816 Vs. 4032 Vs. 6061 Vs. 7075 Aluminum
Understanding the differences between 2618 aluminum and other common aluminum alloys like 2014, 4032, 6061, and 7075 is crucial, as each alloy offers distinct advantages based on its individual mechanical properties and applications.
Characteristic |
2618 Aluminum |
4032 Aluminum |
6061 Aluminum |
7075 Aluminum |
---|---|---|---|---|
Primary Alloying |
Cu, Mg |
Cu, Mg, Si |
Mg, Si |
Zn, Cu, Mg |
Density (g/cm³) |
~2.77 |
~2.69 |
~2.70 |
~2.81 |
Tensile Strength (MPa) |
~440 (T6 temper) |
~380 (T6 temper) |
~310 (T6 temper) |
~570 (T6 temper) |
Yield Strength (MPa) |
~370 (T6 temper) |
~315 (T6 temper) |
~275 (T6 temper) |
~505 (T6 temper) |
Heat Resistance |
Excellent (up to ~200°C) |
Good (up to ~150°C) |
Moderate (up to ~150°C) |
Moderate (up to ~120°C) |
Corrosion Resistance |
Moderate (requires coatings) |
Good (better than 2618) |
Very Good |
Fair (susceptible due to Cu content) |
Machinability |
Good |
Excellent (high Si content) |
Very Good |
Fair (harder due to strength) |
Weldability |
Fair (special techniques needed) |
Poor (due to high Si) |
Excellent |
Poor (prone to cracking) |
Fatigue Resistance |
Excellent |
Good |
Good |
Excellent |
Cost |
High |
Moderate |
Low |
High |
Typical Applications |
Aerospace (engine parts), pistons |
Automotive pistons, engine components |
Structural parts, general use |
Aerospace (frames), high-stress parts |
Key Benefits |
High strength at elevated temps, fatigue resistance |
Wear resistance, low thermal expansion |
Versatility, corrosion resistance |
Exceptional strength, lightweight |
Key Limitations |
Lower corrosion resistance, costly |
Poor weldability, moderate strength |
Lower strength than 7075 |
Poor weldability, corrosion concerns |
2618 stands out with its impressive high-temperature strength and good machinability, making it ideal for demanding tasks like crafting aircraft engine components and high-performance pistons. In contrast, 4032 is favored for engine components due to its low thermal expansion and good wear resistance. 6061, known for its versatility, is found in structural applications, while 7075, with its exceptional strength, caters to high-stress scenarios.
Choosing the right aluminum alloy depends on understanding each application’s specific requirements. Engineers can make informed decisions that optimize material performance and component longevity by carefully evaluating factors like desired strength, operating temperature, and fabrication processes.
Which Alloy Should You Use?
Choosing the right aluminum alloy—2618, 4032, 6061, or 7075—depends on your specific application, priorities, and operating conditions. Below, I’ll break down the decision-making process based on key factors like strength, heat resistance, corrosion resistance, cost, and manufacturability, then provide recommendations for common use cases.
Key Factors to Consider
-
- If you need maximum strength (e.g., aerospace frames), 7075 is the strongest (570 MPa tensile strength).
- For moderate strength (300-400 MPa), 2618, 4032, or 6061 may suffice.
Strength Requirements:
-
- For high-temperature environments (e.g., engine parts, pistons), 2618 excels (up to 200°C).
- 4032 and 6061 handle moderate heat (up to ~150°C), while 7075 weakens above ~120°C.
Temperature Exposure:
-
- If corrosion is a concern (e.g., marine or outdoor use), 6061 is the best choice.
- 2618 and 7075 need coatings due to lower resistance, while 4032 is decent but not exceptional.
Corrosion Resistance:
-
- For welding or forming, 6061 is the easiest to work with.
- 4032 is great for machining but poor for welding.
- 2618 and 7075 are harder to weld and form due to their composition.
Manufacturability:
-
- 6061 is the most cost-effective and widely available.
- 2618 and 7075 are pricier due to their specialized properties, with 4032 falling in between.
Cost:
-
- 4032 stands out for wear resistance (high silicon content), ideal for moving parts like pistons.
Wear Resistance:
Quick Decision Guide
- Prioritize Strength: Go with 7075 Aluminum.
- Prioritize Heat Resistance: Choose 2618 Aluminum.
- Prioritize Wear Resistance: Pick 4032 Aluminum.
- Prioritize Versatility/Cost: Select 6061 Aluminum.
If you have a specific use case in mind (e.g., part type, environment, budget), let me know, and I can refine the recommendation further!
Conclusion
In conclusion, mastering 2618 alloy aluminum requires a deep understanding of its composition, properties, and practical applications. This high-performance alloy, favored in aerospace and motorsports, offers exceptional strength and durability for high-temperature environments. By comparing it to other alloys like 7075 and 6061, you can make informed decisions on its use. Remember, 2618 alloy aluminum’s unique characteristics make it a top choice for critical applications where strength and reliability are paramount. If you’re considering utilizing this alloy, seek expert advice and get quotes to ensure success in your projects.
Why Choose Linsy Aluminum
As one of the leading aluminum brands and a top supplier in China, Linsy Aluminum emphasizes quality and reliability in all its products. Our advanced aluminum factory in China manufactures high-performance aluminum alloys that satisfy the toughest industry requirements. Dedicated to excellence, we provide precision, durability, and tailored options to accommodate your specific project needs, establishing us as a trusted partner for businesses globally searching for exceptional aluminum solutions. GET A QUOTE
Frequently Asked Questions
What is the difference between 4032 and 2618 aluminum?
While both are heat-treatable aluminum alloys commonly used for pistons, 4032 aluminum prioritizes lower thermal expansion and good wear resistance. In contrast, 2618 aluminum excels with higher strength at elevated temperatures, as indicated by their respective specifications.
What is the difference between 2024 and 2618 aluminum?
Both are high-strength aluminum alloys, but 2024 aluminum offers higher strength at room temperature, while 2618 aluminum maintains its strength better at higher temperatures, making each suitable for different applications as per their specifications.
What is the difference between 7075 and 2618 aluminum?
7075 aluminum boasts significantly higher strength than 2618 aluminum but falls behind in high-temperature applications. 7075 is favored for structural components requiring maximum strength, while 2618 suits high-heat situations as outlined in their respective specifications.
How Does 2618 Alloy Compare to Other Aluminum Alloys in Terms of Strength and Durability?
2618, while not the strongest aluminum alloy, shines in high-temperature strength and durability. Compared to others, it maintains its mechanical properties better under heat, making it ideal for demanding environments.
What Makes 2618 Alloy Ideal for Aerospace Applications?
2618 aluminum’s specifications highlight its high strength-to-weight ratio and excellent high-temperature performance, making it ideal for aerospace components that must be both lightweight and withstand extreme conditions.
Can 2618 Alloy Aluminum Be Recycled or Reused in Other Industries?
Like many aluminium alloys, 2618 is recyclable. While primarily used in aerospace, its valuable properties find reuse in industries seeking high-temperature resistance and strength, making it a versatile material.